


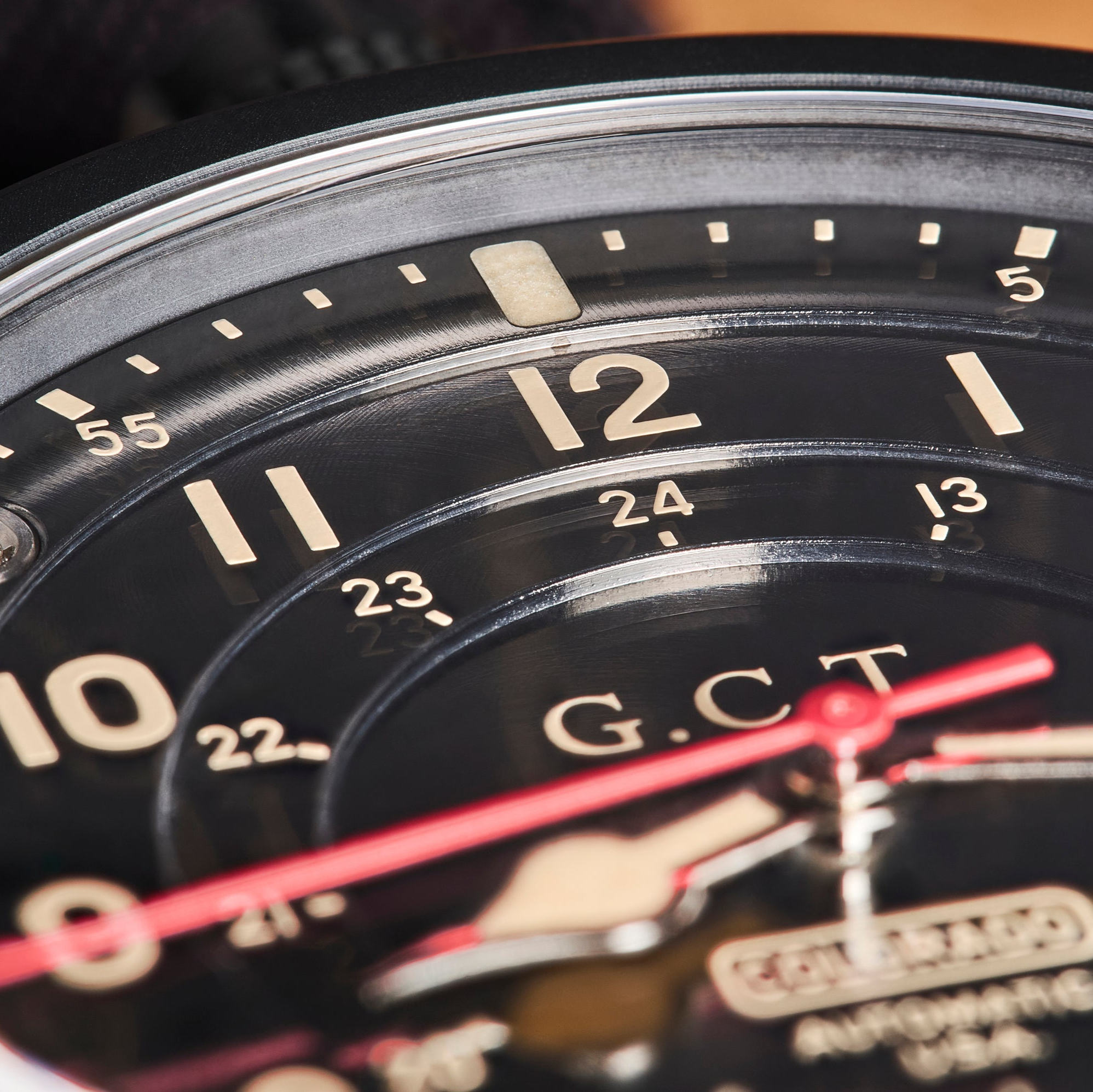


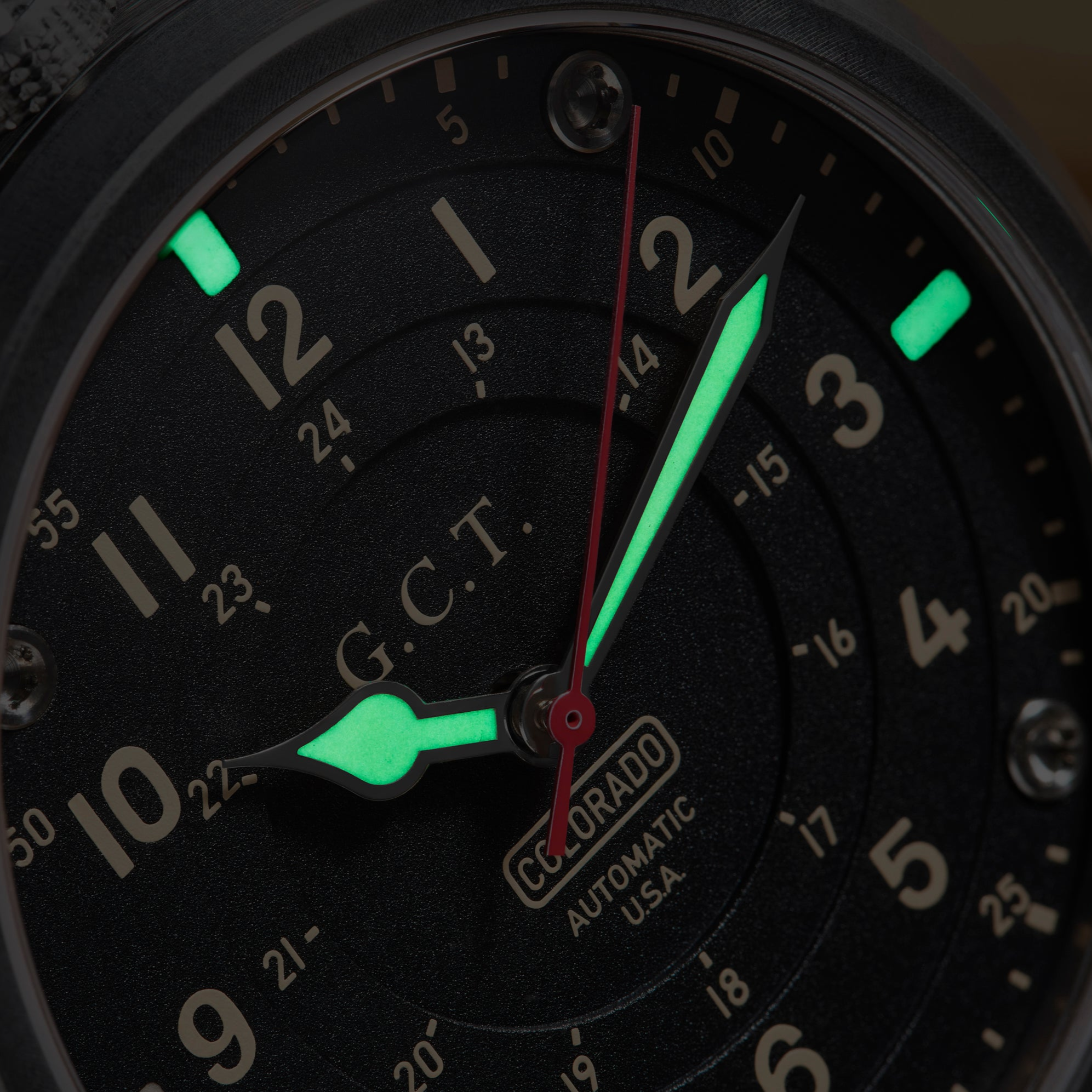
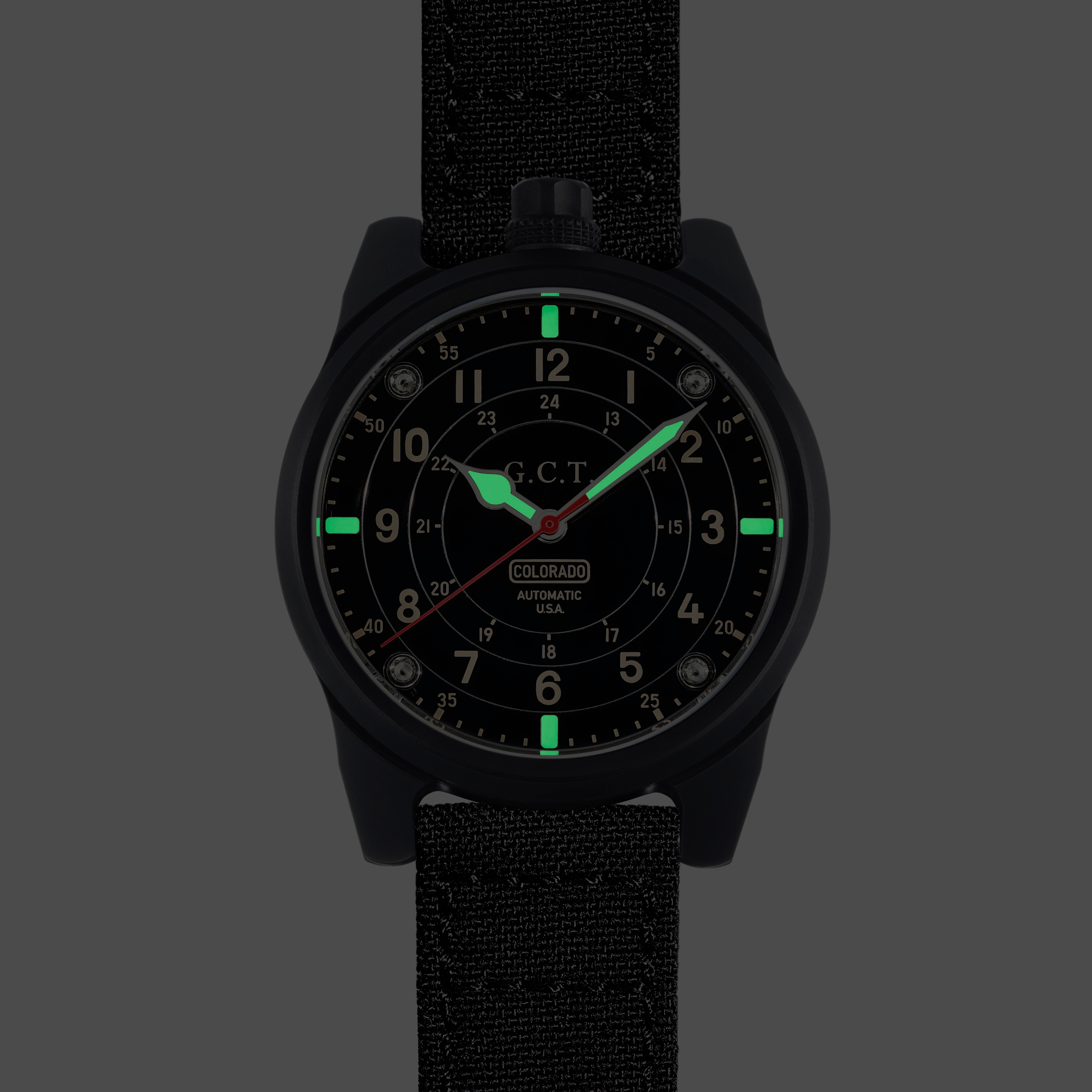
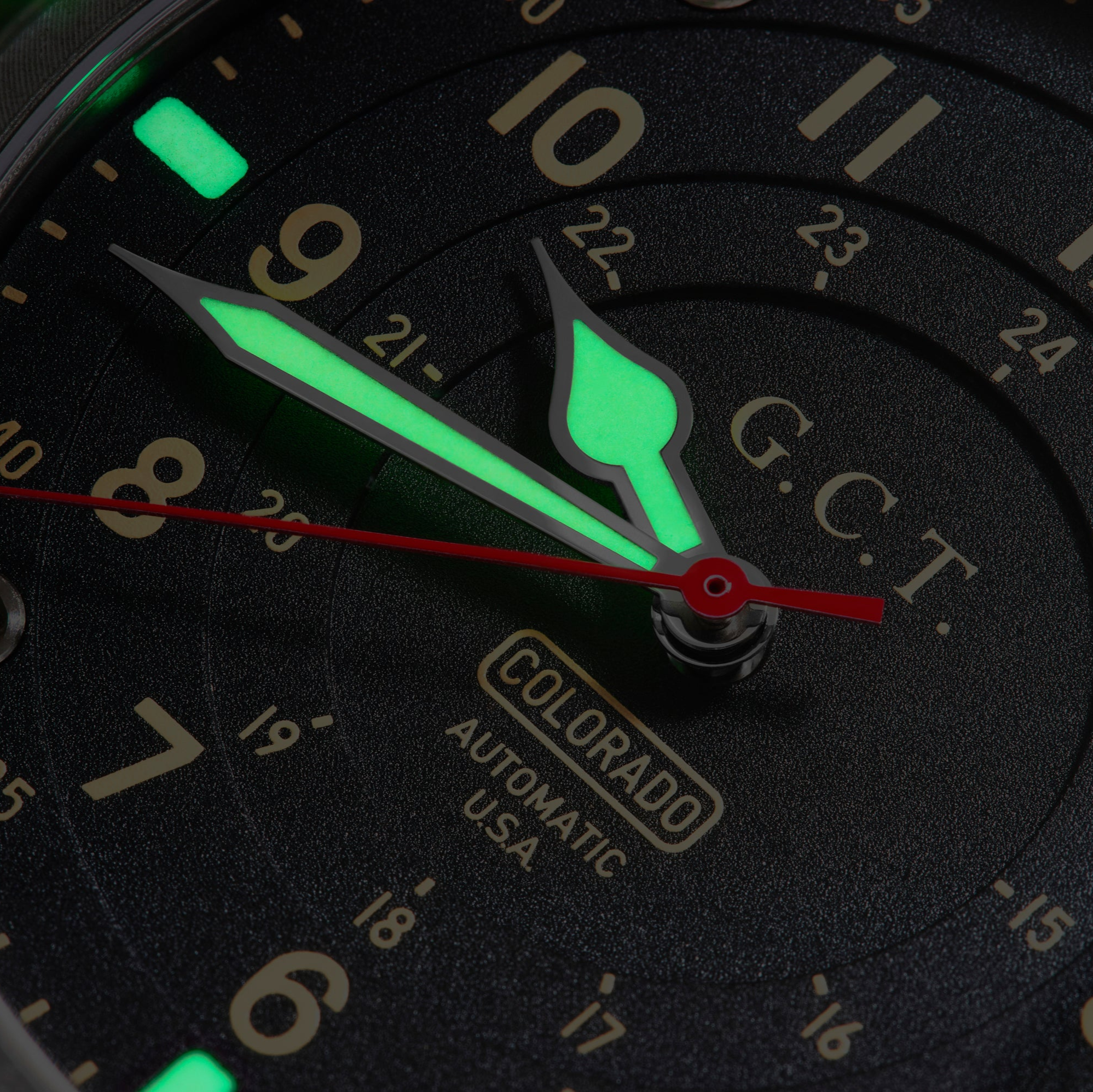
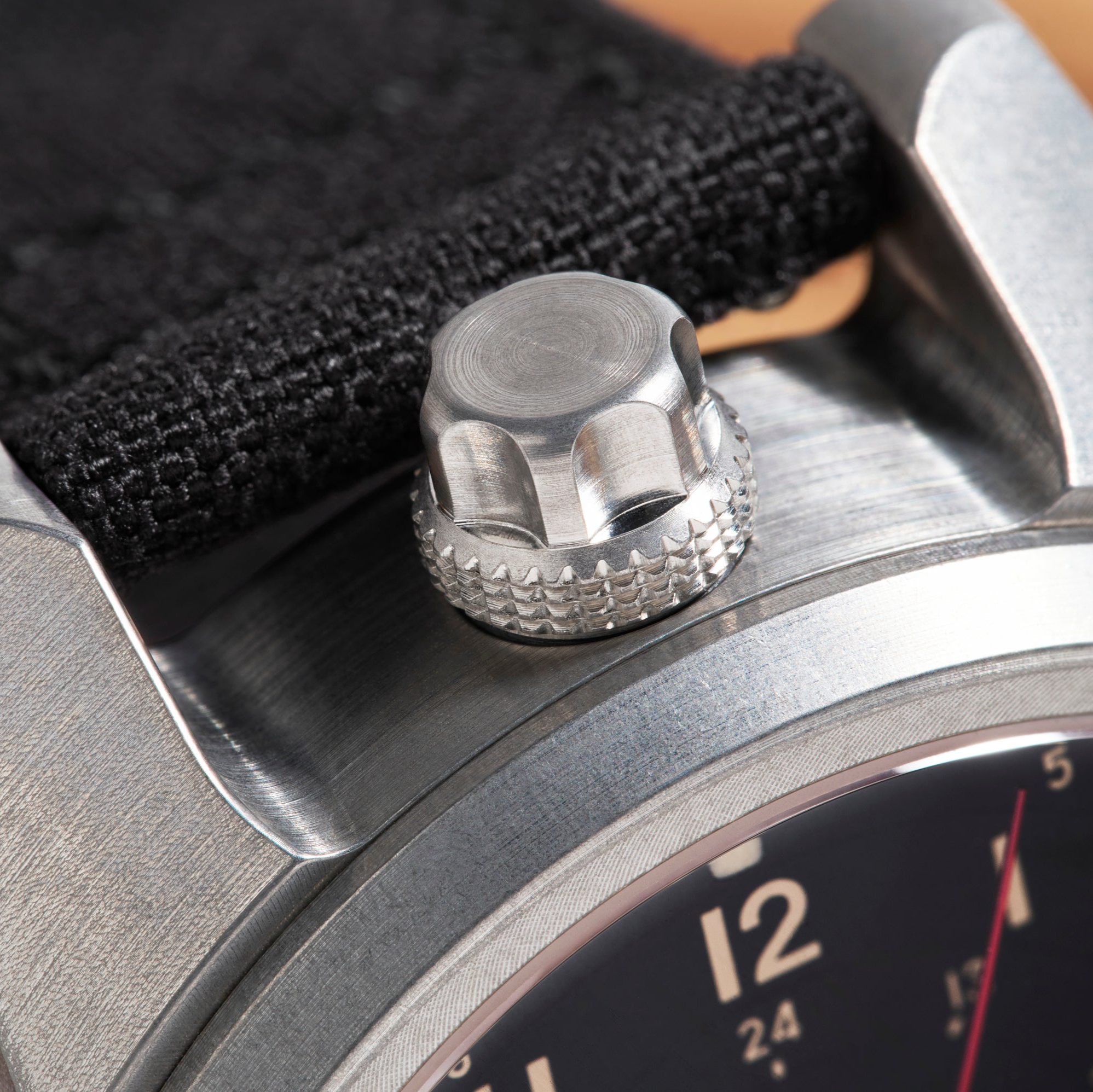




The GCT - Steel Case - Machined Dial
Case & Dial:
Steel Case - Machined DialThe 42mm diameter, 13mm thick stainless steel case was cut from a block of metal in Colorado with you in mind. We inlayed the case-back to make it very comfortable and stonewashed the case so it shows less wear. We added heavy knurling to the crown to make it easy to wind, and yes, it's a screw-down crown to increase the water resistance! The GCT features an automatic movement with 42 hours of power reserve though, so you won't have to wind it often, but you might want to since it feels so smooth...
85% American Made
2-Year Warranty
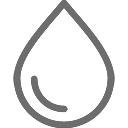
WR to 150 meters
Choose options



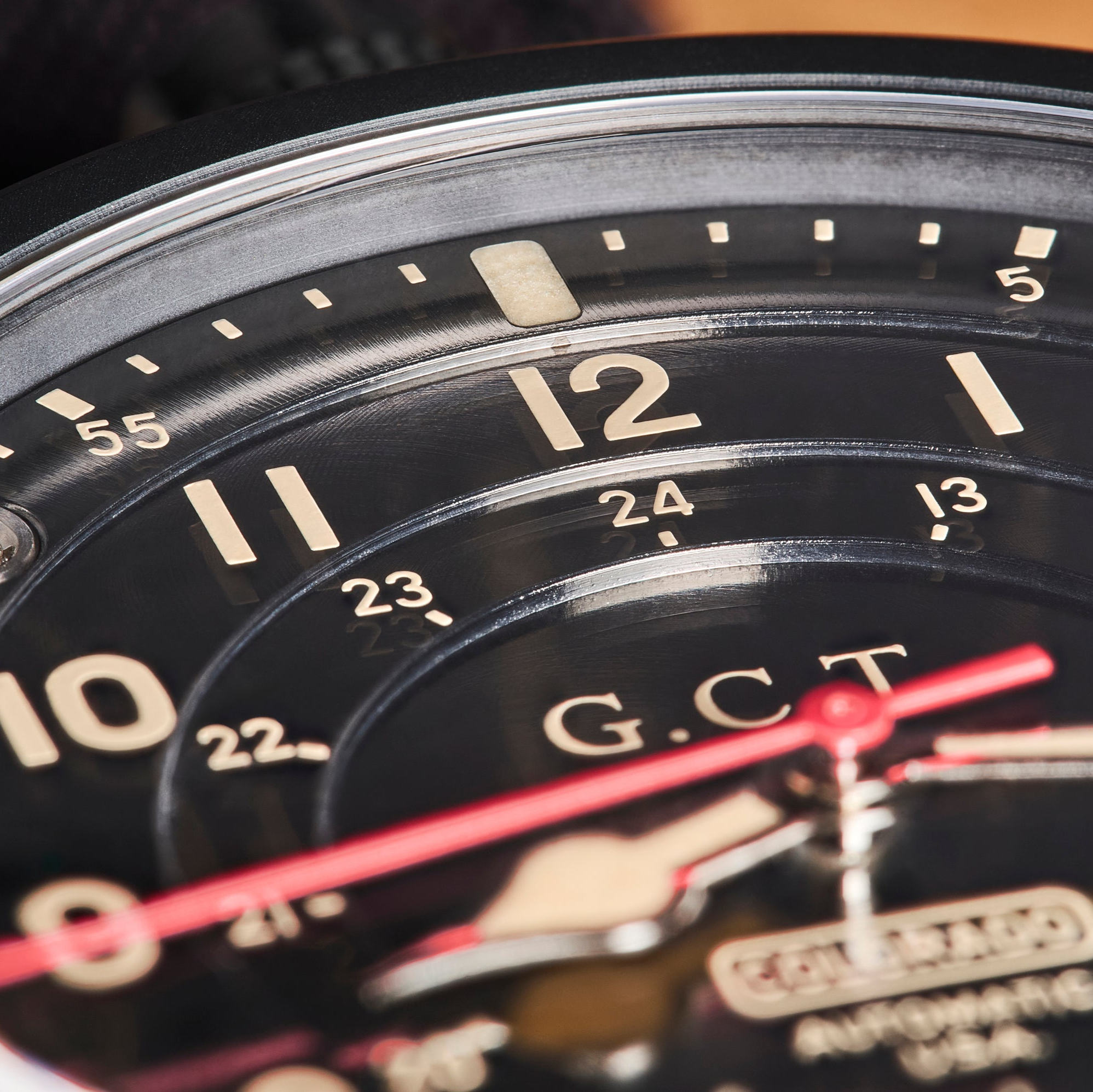


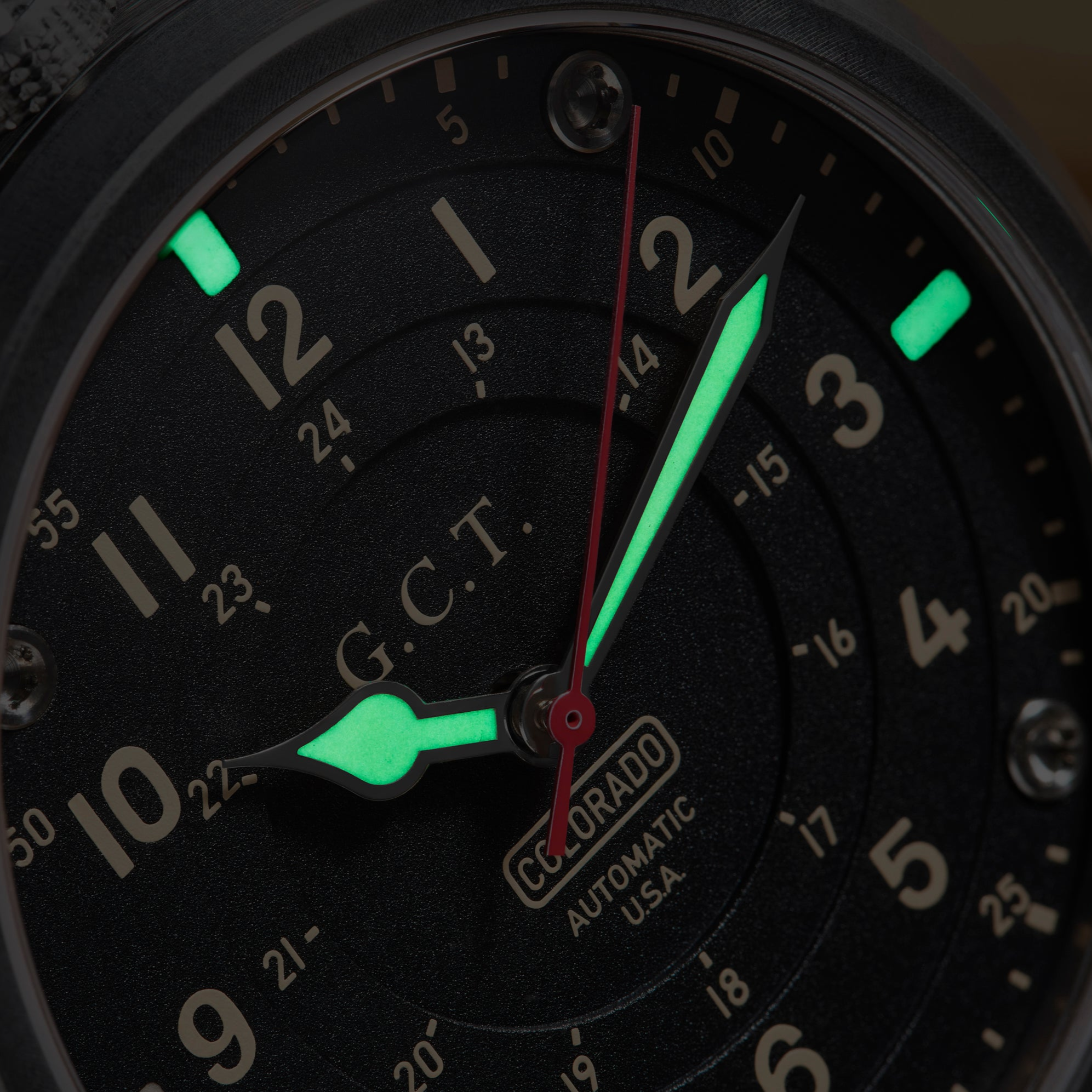
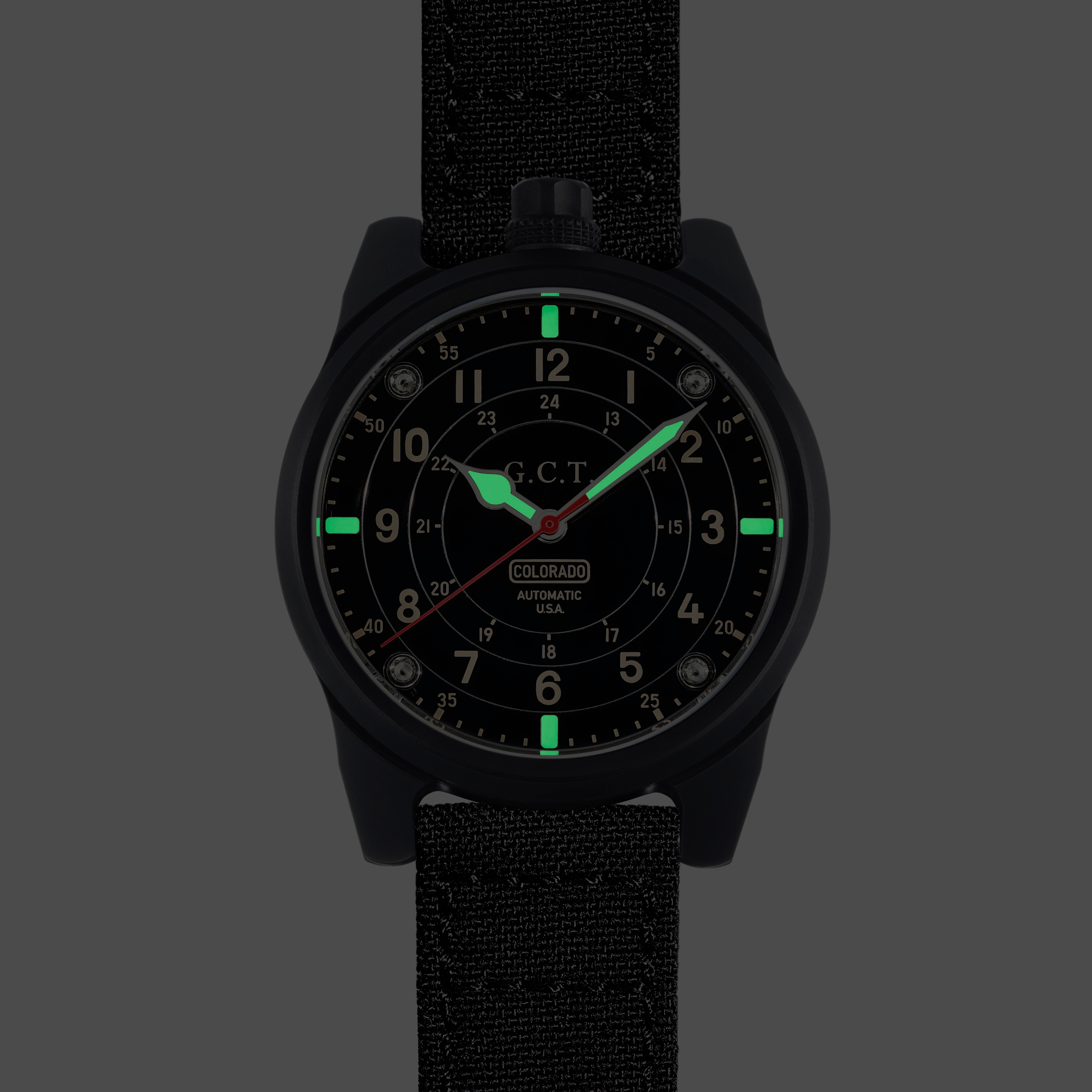
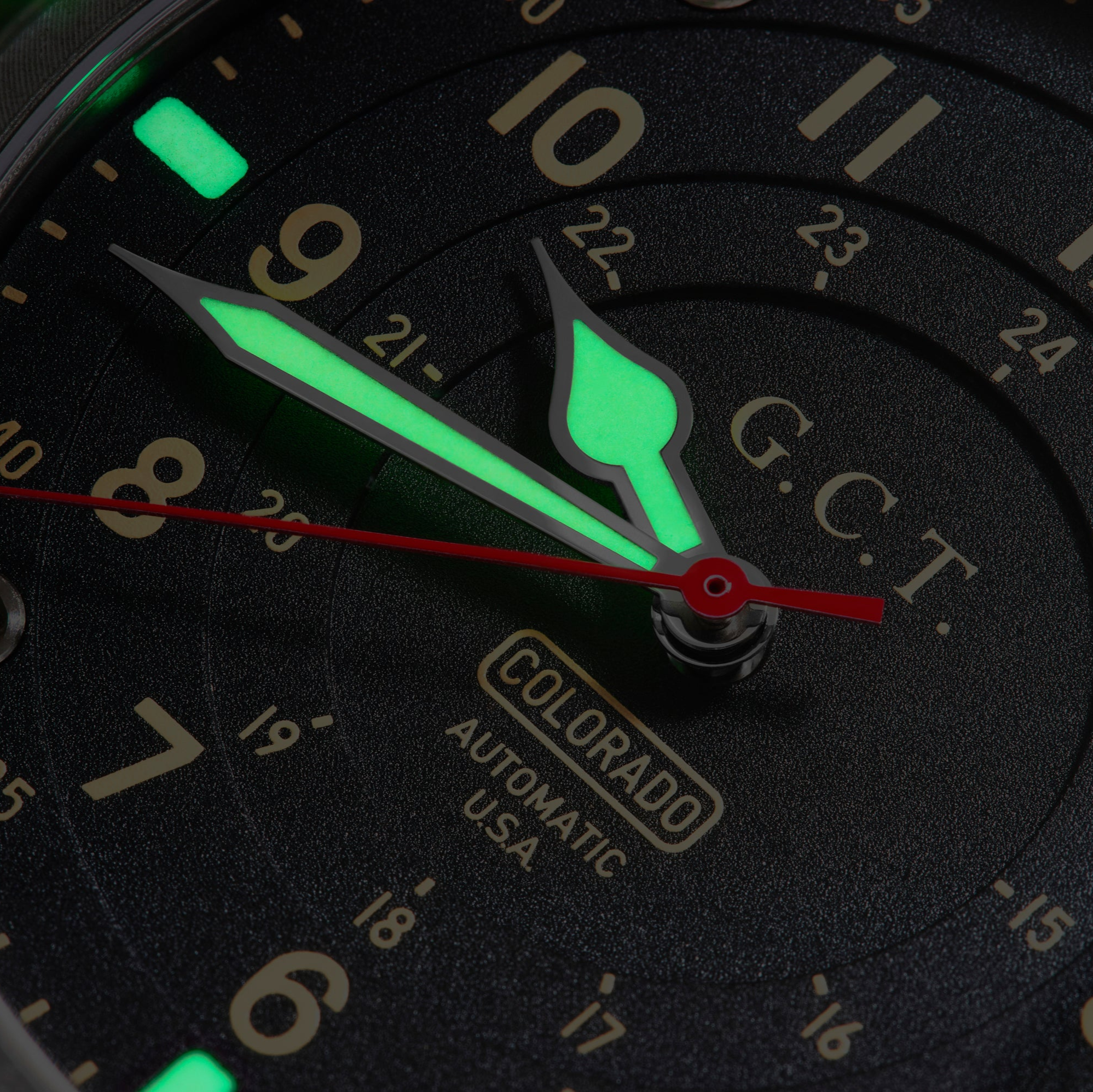
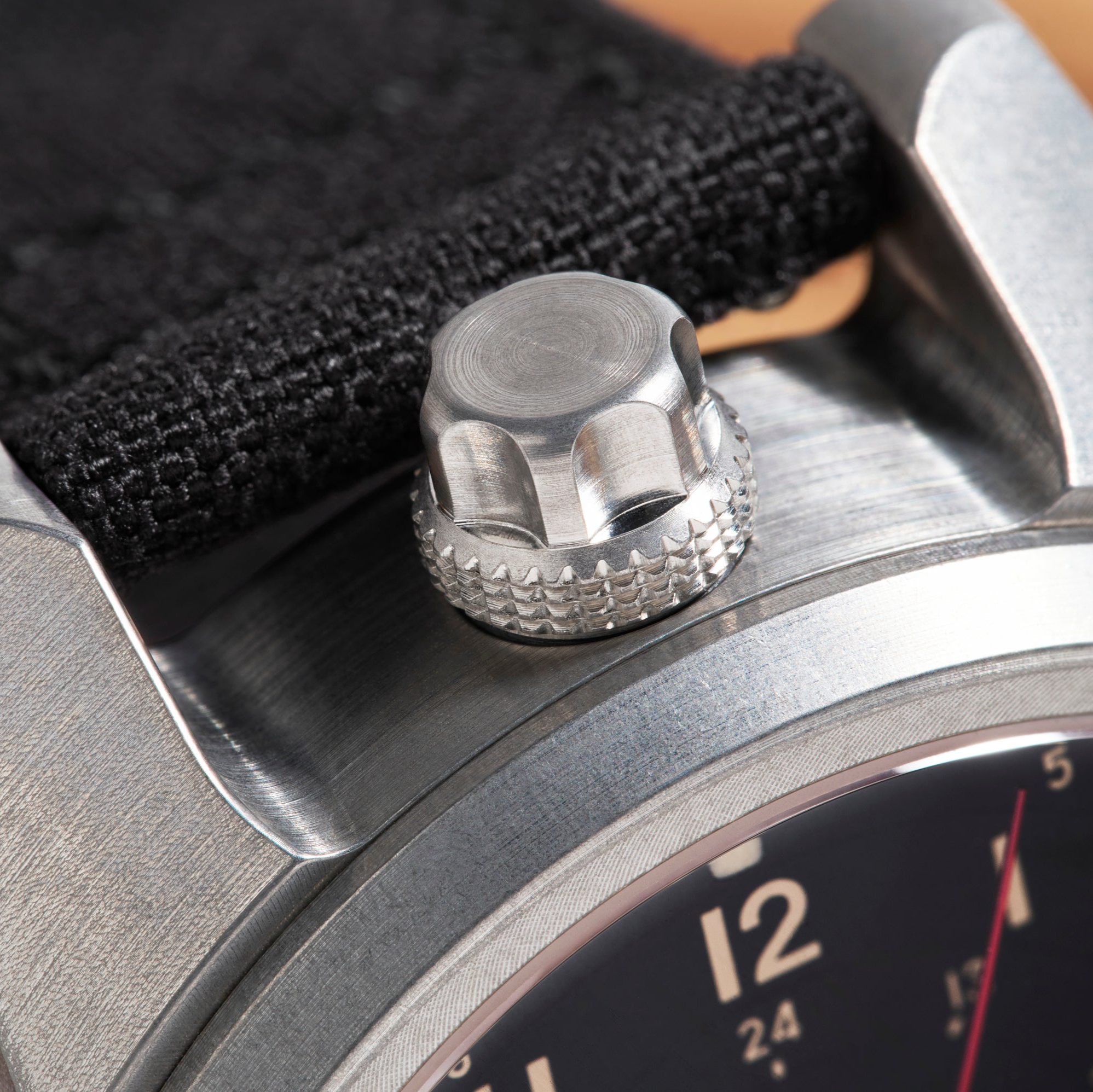




Case & Dial:
Steel Case - Machined DialWhat Comes With The GCT?
But Wait... There's More!
Your GCT watch ships inside a waterproof Seahorse box that’s also Made in USA! We include one black strap in the top lid of the box for you to put on with the quick release springbars! Currently we have black, green, and khaki straps, but it’s a standard 20mm quick release connection, so you can put anything you’d like on this watch!


Live Life. This Watch Will Keep Up.
Built to Last A Lifetime
The 42mm diameter, 13mm thick stainless steel case was cut from a block of metal in Colorado with you in mind. We inlayed the case-back to make it very comfortable and stonewashed the case so it shows less wear. We added heavy knurling to the crown to make it easy to wind, and yes, it's a screw-down crown to increase the water resistance! The GCT features an automatic movement with 42 hours of power reserve though, so you won't have to wind it often, but you might want to since it feels so smooth...

Doing What No One Else Does.
A Dial Made For You
Making watch dials is extremely difficult. We found out the hard way why no one else does this at scale in the United States. But, after hundreds of prototypes, we figured it out. The GCT dial is cut from aluminum here in Fort Collins, Colorado and a diamond-like carbon black coating is applied by a supplier before it's printed back here in-house. We even cut pockets at the four quadrants so we can hand-apply lume to give you a legible and functional design like no other.

Day

Night

Using The Right Protection
Sapphire Crystals
We scoured the country for the best glass suppliers and after years of searching we found someone to make sapphire glass for us in New Hampshire. So far we’ve only been able to find flat crystals Made in USA, so the GCT has a flat American sapphire crystal on the back, and a domed foreign sapphire crystal on the front. These sapphire crystals protect the dial and movement inside the watch while being almost perfectly clear so you can see all the beauty inside.

Strap In And Buckle Up
Straps & Buckles
Our straps are made from Cordura, an especially durable synthetic canvas material that the military has used for its toughness. Every watch comes with one black strap and our in-house machined stainless steel buckle.
The Cordura straps have a quick-change spring bar, making swapping the strap easy. You can add a green or khaki strap to your order at checkout, or you can easily swap our strap for any 20mm quick-release strap you’d like.
The Cordura straps and the buckles on our extra (free) straps are made overseas for now, but we hope to find a domestic Cordura supplier and scale up our buckle manufacturing soon.
It's What's Inside That Counts
Automatic Movements Assembled In Arizona
The team at FTS designed a new caliber and invested in the facility and equipment necessary to assemble movements right here in the USA. On top of that, they're training a neurodiverse workforce to build and service watches.
FTS is the perfect movement partner for Colorado Watch Company because they focus on quality, value, and scalability, plus, they’re committed to continuously making more and more in America. For this reason and because there literally is no other American movement at scale, they call their new movement the "Americhron."
As we scale together, Colorado Watch Company will focus on manufacturing the components, and FTS, using their team of skilled artisans, will assemble not just the movements but also the final watches in their facility in Arizona. Teamwork makes the American Dream work.
If you look closely, you can see the movement under the rotor on the GCT watch is actually gun-metal in color. We do this to further differentiate the GCT from our Field Watch.
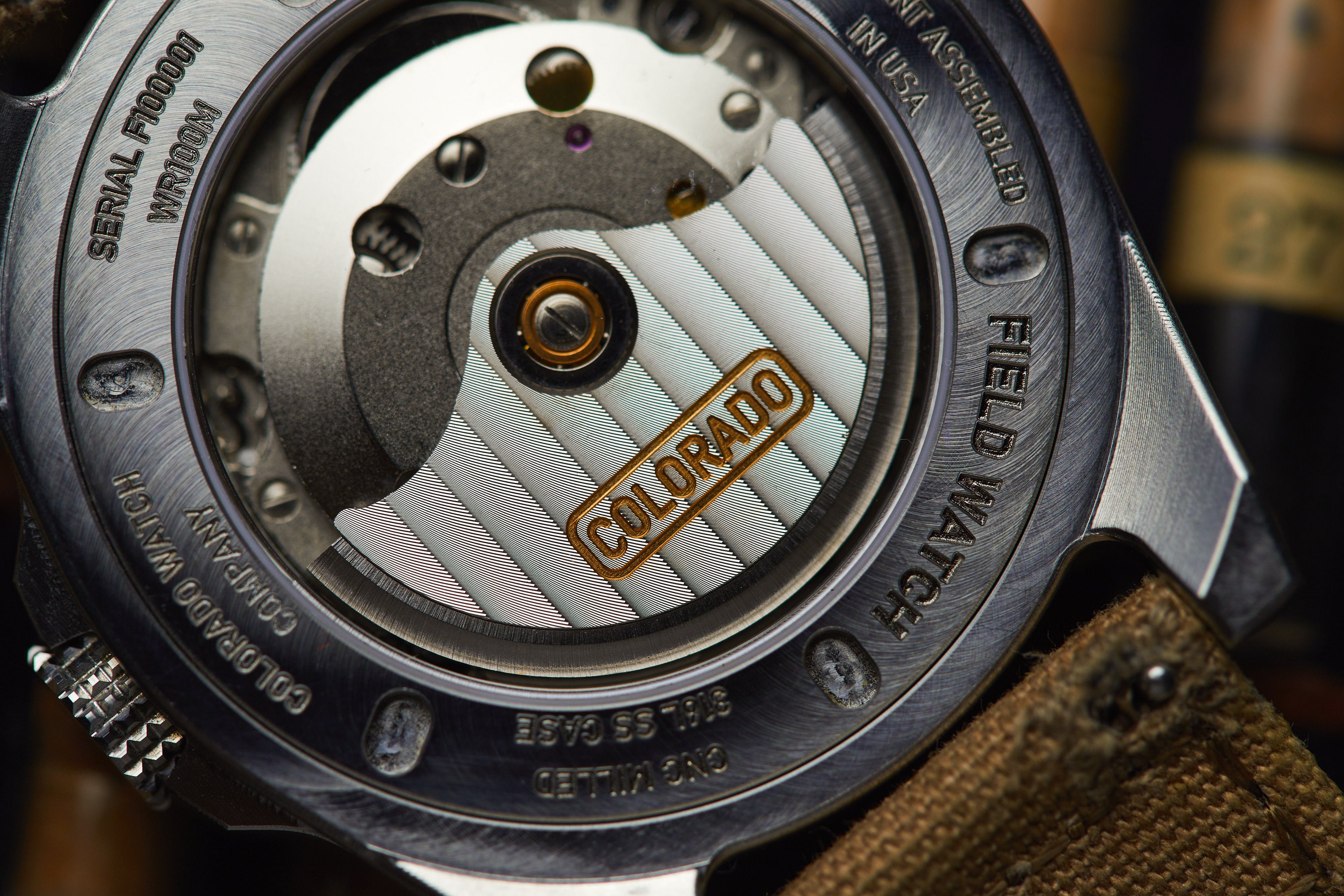
Let customers speak for us
Transparency and Integrity
How it's Made
We can't make statements like "the most American watch at scale today" and "Built in the USA one batch at a time" and not back it up. That's why we like to SHOW you, not just tell you. Scroll down if you'd like to see exactly how we make our watches as well as where we make and source all the components!
We are proud to say that 85% of the cost to build the GCT watch is American. We say Built in the USA because we're doing everything we can to source the components from the United States, but it’s extraordinarily difficult. When we can't find a domestic supplier, we're committed to being transparent so you know exactly what you're getting when buying a watch. When you invest in a Colorado watch, you are directly supporting the future of American manufacturing. Our mission is to make 1% more of these watches here in the USA every year. It may take us 15 years, but we believe we can make 100% of the watch in the United States.

Making the Case For A Truly American Watch
The Stainless Steel Case
The cases, bezels, and case-backs of both watches are CNC machined from 316L stainless steel billet here in Colorado. We start from scratch and cut each case one at a time, because we think that's the best way to get something that'll last a lifetime. We like to say "we're Engineers, not Watchmakers," and if you watch our YouTube videos about how we make these parts, you'll see why.
The Steel option for both cases maintains some of the machined finish even after we stone-wash it, so you can see the tool marks from the process of making the case. These marks are made by a small carbide cutting tool spinning at high RPMs and slowly shaving away the material that doesn't belong.
It's Always A Great Day To Cut Metal
CNC Machining
Computer Numerical Control (CNC) Machining is not "the easy" or "the cheap" way to do it, but it allows us to make extremely accurate parts and have complete control over the design of our products.
Currently, the case starts as a 2 inch "puck" of solid stainless steel. From there, we "prep" our stock to make it compatible with a dovetail vise fixture. This "pre-op" allows us to hold the material extremely rigidly and increases our precision and repeatability. After that, the prepped puck goes into the dovetail vise on our 5-axis mill, a DMG Mori DMU50.
Watch the YouTube video above though to see how we make our cases now, and how we plan to make them in the future. Our new Tsugami mill-turn machine is going to change the game and allow us to make multiple batches (hundreds) of watches a month!



Diamond-Like Carbon
The DLC-black coating
Our DLC-black (Diamond-Like Carbon) cases go a step further though. DLC is an extremely tough coating that is trusted in many industrial applications such as high-end firearms. DLC coatings are a subset of PVD or Physical Vapor Deposition coatings. This process uses electricity in a sealed chamber to deposit a thin film of material with hardness and scratch resistance similar to diamond… hence the name.
After machining and stone washing here in Colorado, the case is sand-blasted with fine grit media and DLC coated in California by a supplier. This coating creates a highly durable, dark, matte-black finish.
We use the same process on the dials for the GCT watch, but the dials are made from aluminum, so the final appearance is slightly different.
Just wait until we get dialed in
Dials Made in Colorado
The dials are machined from plates of aluminum on our 5-axis CNC mill. We made a custom window-machining fixture so we can rigidly hold the material while we cut the metal into a disc and slice the layers into the dial to create this unique look.
One of the advantages of machining our dials is that if we want to do something "weird" like cut holes in the dial and affix it to the case with four small screws, because, well, that's really cool... we can do that! Did we mention we make the screws too?
After machining, the GCT dials are lightly tumbled to remove debris and then the black DLC coating is applied by a supplier of ours. The Machined dial is coated as is to give it a "fresh off the machine" look, and the Matte dial is sandblasted before it's coated to remove all the machine-marks and become ultra-legible.
Finally, the dial artwork is pad-printed using our new Swiss pad-printing machine. The machine places ink inside a negative of our dial, also known as a cliche. Then, it uses a silicon pad to pick up this negative and transfer it to the dial with fine accuracy.


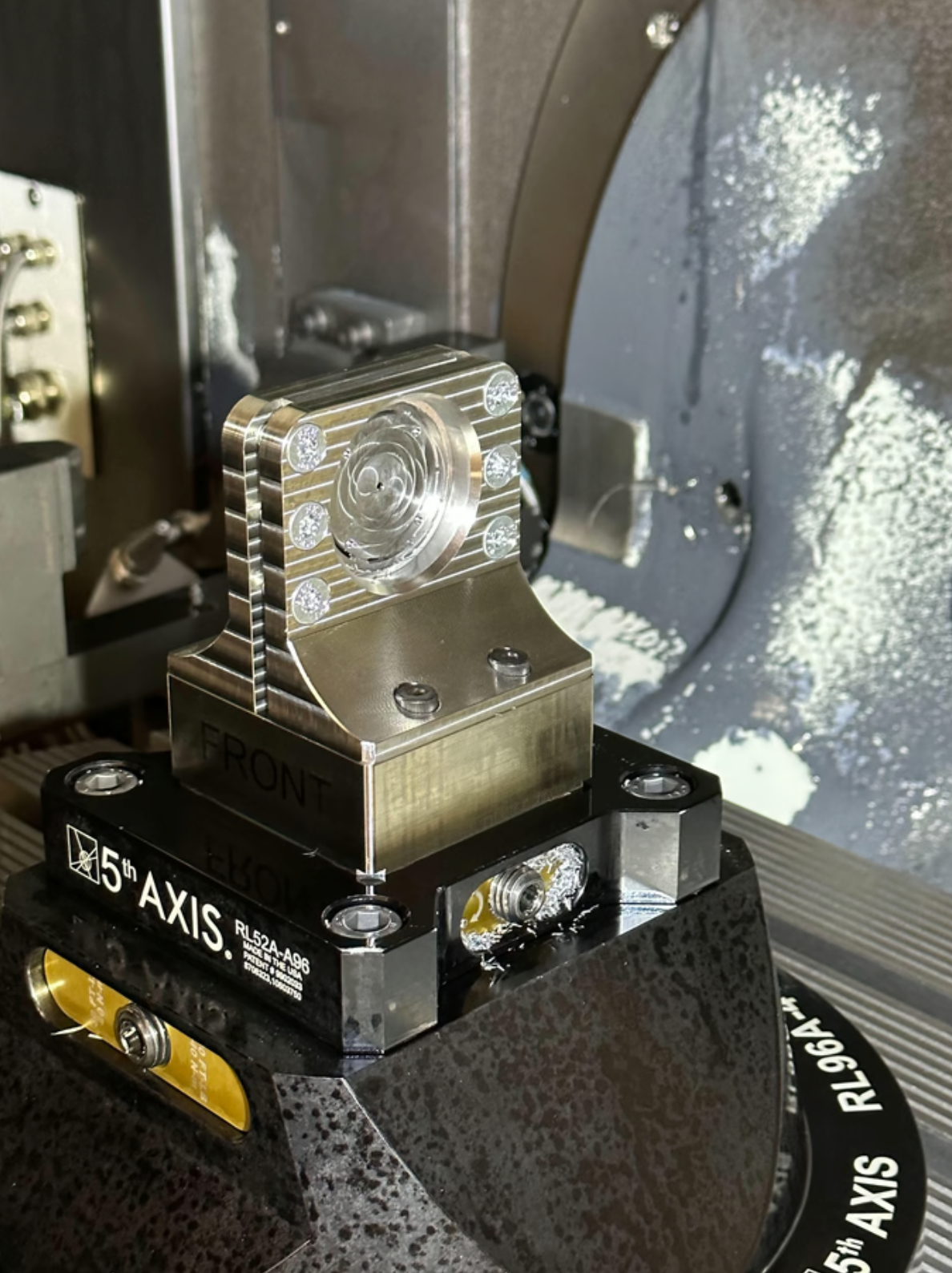

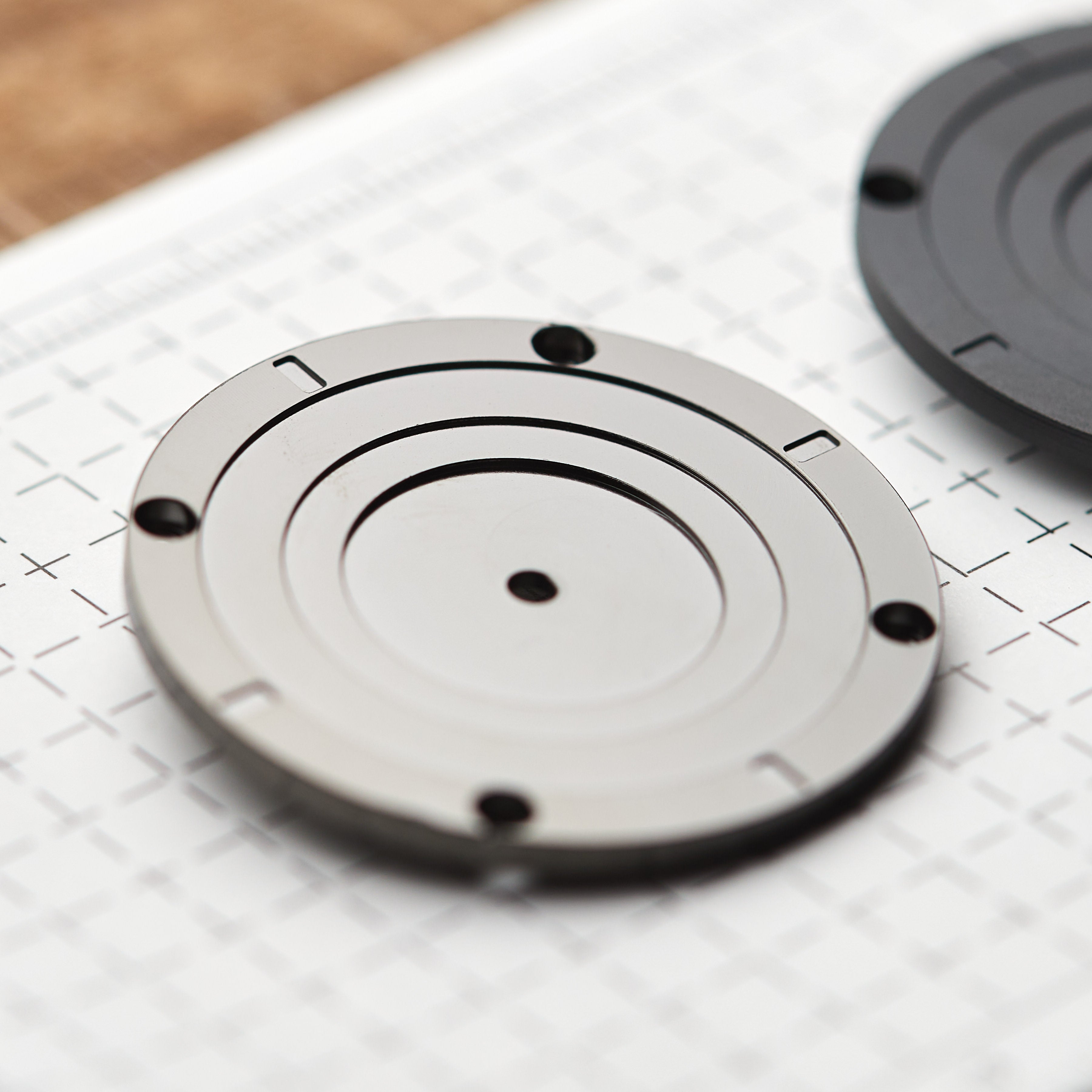
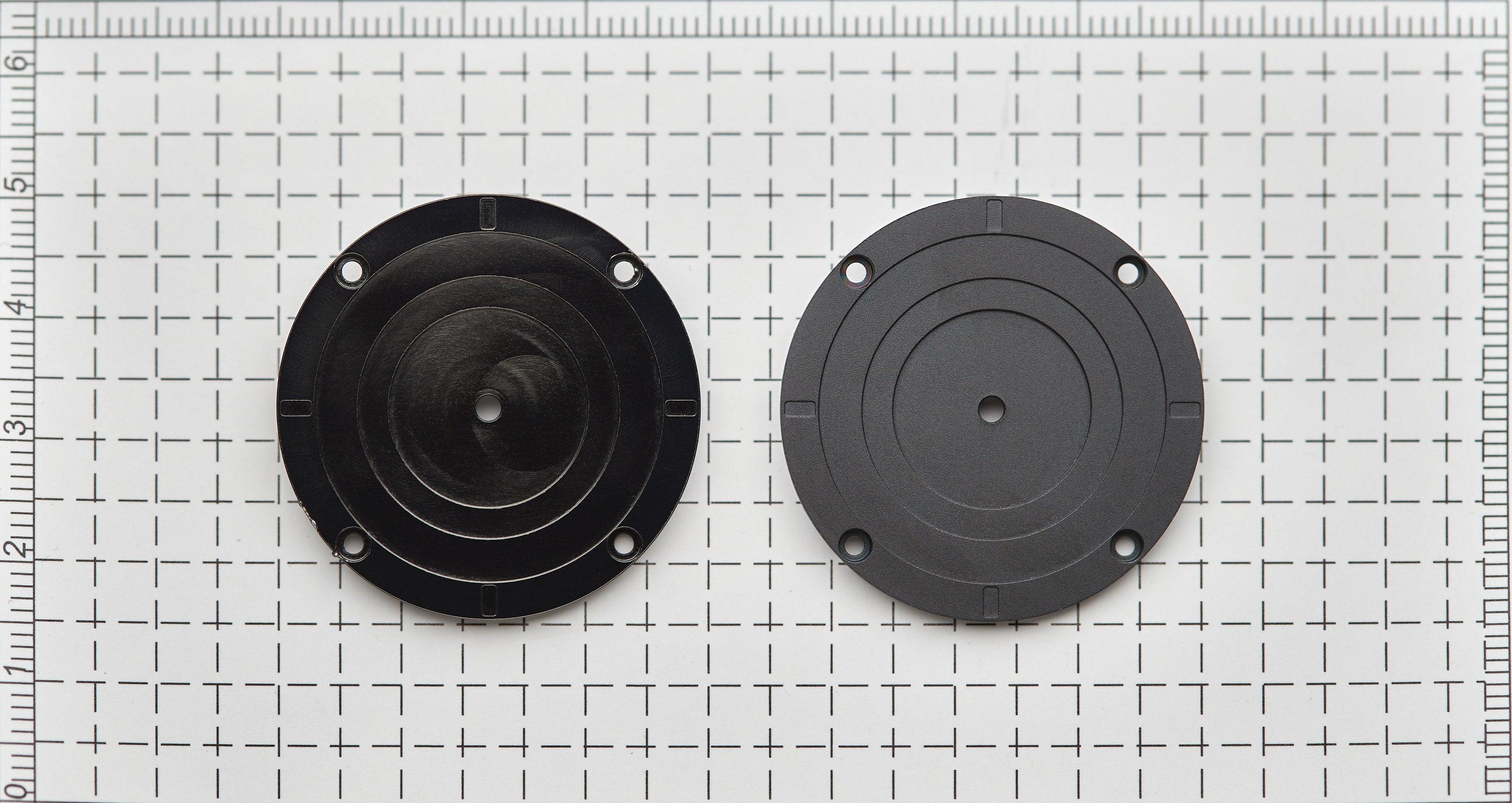
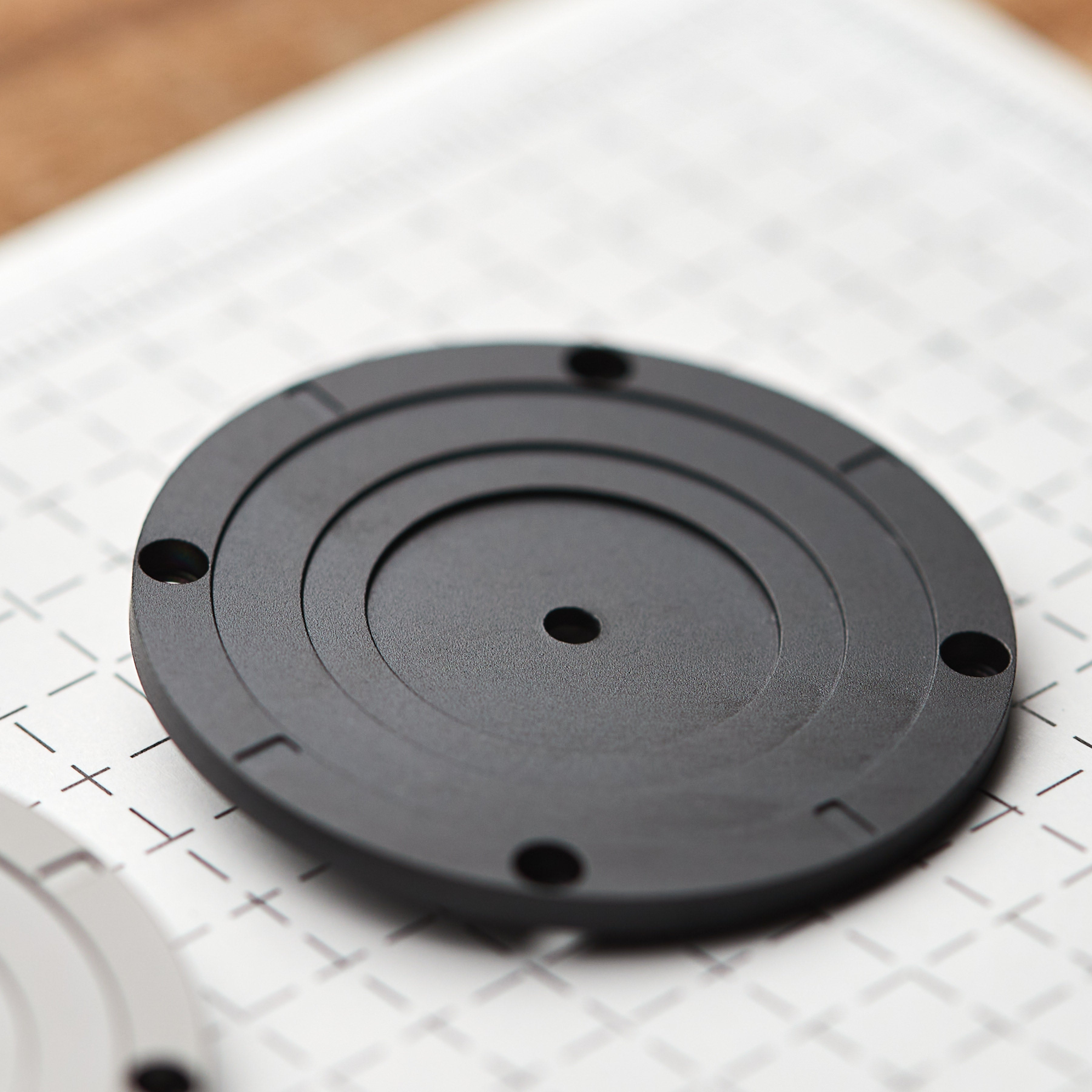



We get all wound up about this part
The Crown
The crown is the knob outside the case used to set and wind the watch. The screw-down crown and case tube parts for the GCT are machined from long bars of stainless steel on our Swiss turning center CNC machine which was actually made in Italy. Swiss-style lathes are commonly used in the watchmaking industry when high levels of accuracy are required for small round parts.
After we load a new bar, the spindle spins the material at up to 10,000rpm while it carves away metal to find the part's final form. When the first operation is finished, a spindle facing in the opposite direction, known as a sub-spindle, moves forward and grabs onto the part.
The machine then cuts off the part and finishes the back side while the machine simultaneously starts a fresh first operation on the main spindle. Our machine has a parts catcher and a small conveyor belt that we love to watch spit out finished parts.
Our engineer, Sky has poured himself into learning to program this extremely complicated machine despite much of the manual being in Italian or broken English! These finished parts speak for themselves though. From the machined knurl and rounded flutes of the GCT crown to the laser-engraved flag on the Field Watch crown, we're very proud of these products.
You just have to see the back though
The Exhibition Case-Backs
We chose to make an exhibition case-back for our watches to show off the beautiful automatic, mechanical movement. We also recessed the case-back flush with the case, so it wears comfortably and is as thin as possible.
We've been engraving our case-backs in-house for our Vortic brand since 2015, and last year, we bought a new laser engraving machine that we're very excited about. It's a German machine made by Foba, and it uses a vision system to "see" the parts and make extremely accurate and high-quality marks.
Each case-back is engraved with the model year and a unique serial number.


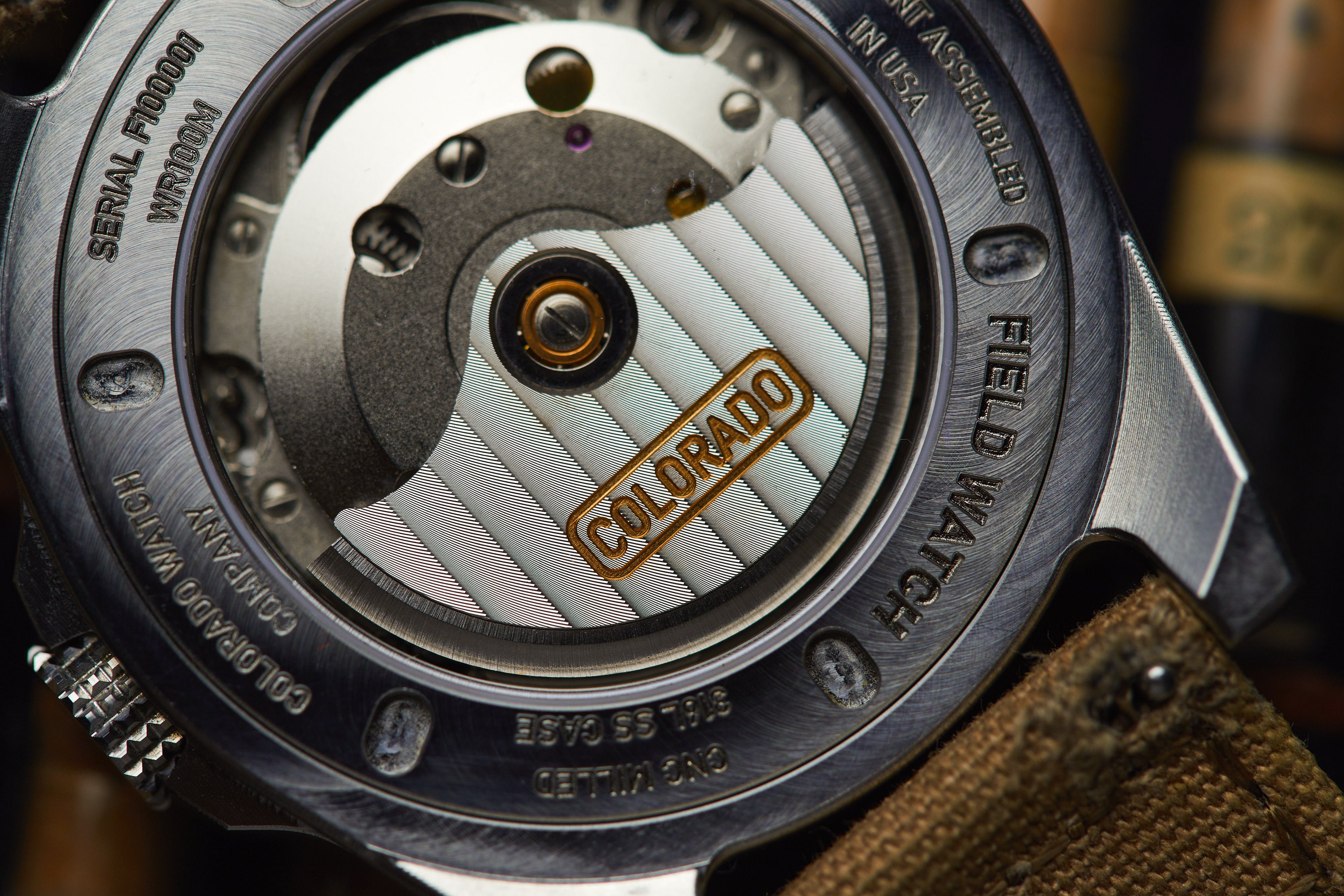

Need help?
Frequently Asked Questions
Yes, we ship all over the world! Shipping costs and import taxes will apply, but you should see more about those at checkout.
We do best via email at info@coloradowatchcompany.com, and we typically respond within 2 business days.